Table of Contents
The Potential of Stainless Steel in Hydrogen Production
Stainless steel is increasingly recognized as a game-changer in hydrogen production, especially in key methods such as steam methane reforming (SMR) and electrolysis. In SMR, where natural gas is converted into hydrogen under high temperatures and pressures, stainless steel’s exceptional resistance to heat and corrosion makes it an invaluable material.
Reformers, heat exchangers, and other critical components in this process demand materials that can withstand extreme conditions without degrading. Stainless steel’s durability not only ensures long-term performance but also reduces the need for frequent maintenance, which in turn lowers operational costs.
In the case of electrolysis, which splits water into hydrogen and oxygen using electricity, stainless steel plays a pivotal role in the construction of electrolyzers. Given the highly corrosive nature of the electrolytic environment, stainless steel’s ability to maintain its integrity under such conditions makes it an ideal choice. Moreover, advancements in stainless steel alloys have enhanced their performance, enabling more efficient, scalable hydrogen production.
As the global push for clean energy intensifies, stainless steel’s role in facilitating cost-effective and sustainable hydrogen production technologies positions it as a cornerstone in the green energy transition.
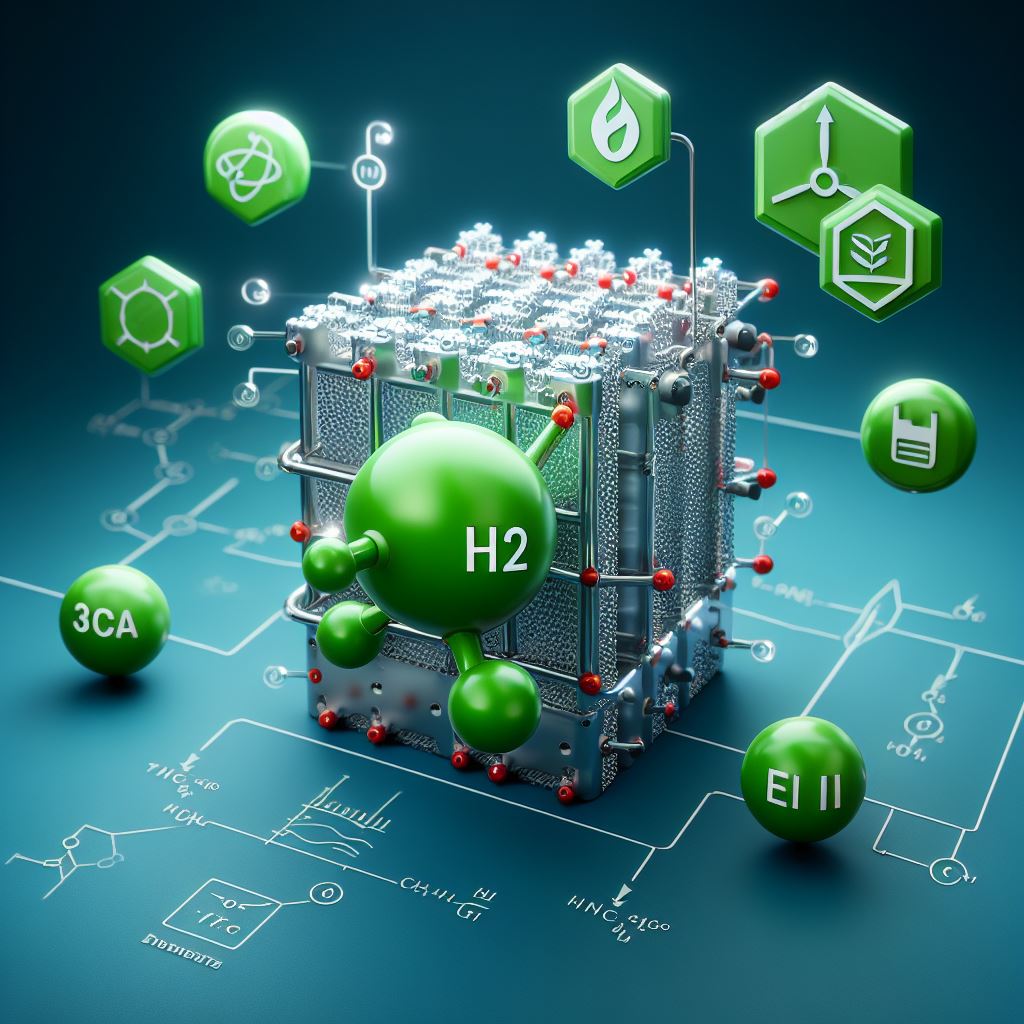
Stainless Steel’s Role in Steam Methane Reforming
In the realm of steam methane reforming, stainless steel shines in the construction of reformers and heat exchangers. Its exceptional ability to withstand high temperatures and corrosive environments makes it a cornerstone material in this hydrogen production technique.
Stainless Steel’s Significance in Water Electrolysis
In water electrolysis, stainless steel plays a vital role in the construction of electrolyzers. Its corrosion resistance and durability make it a preferred choice for enduring the harsh electrolytic environment of the process.

Green Hydrogen Innovation from Our Oceans
A groundbreaking initiative led by Professor Mingxin Huang at the University of Hong Kong’s Department of Mechanical Engineering introduces a novel stainless steel variant. This innovation exhibits robust corrosion resistance, opening doors for the production of green hydrogen from seawater, a readily available resource.
While the cost of this new stainless steel is significantly lower than its counterparts, its performance in a saltwater electrolyzer rivals that of the industrial practice using titanium. This breakthrough involves the addition of a secondary manganese-based layer onto the existing chromium-based layer, challenging conventional corrosion science understanding.
The Mn-Based Passivation Mystery
The scientists, led by Dr. Kaiping Yu under Professor Huang’s supervision, initially hesitated due to the common belief that manganese diminishes stainless steel’s corrosion resistance. However, atomic-level results presented a convincing case, unveiling the counterintuitive Mn-based passivation mechanism.

Revolutionizing Production Costs
Presently, a 10-megawatt PEM electrolysis tank system costs approximately HK$17.8 million (USD $2.8 million), with over half attributed to structural components. Professor Huang’s innovation allows stainless steel to replace expensive elements like gold and platinum, potentially reducing structural material costs by around 40 times.
“From experimental materials to real products, such as meshes and foams for water electrolysers, there are still challenging tasks at hand. Currently, we have made a significant step toward industrialization,” explains Professor Huang. The team has already collaborated with a Mainland factory to produce tons of SS-H2-based wire, progressing towards more cost-effective hydrogen production from renewable sources.
Beyond Hydrogen: A Legacy of Stainless Steel Innovations
Huang’s research team, known for their 2021 anti-COVID-19 stainless steel and the 2017/2020 developments of ultra-strong and ultra-tough Super Steel, continues to push the boundaries of stainless steel applications.
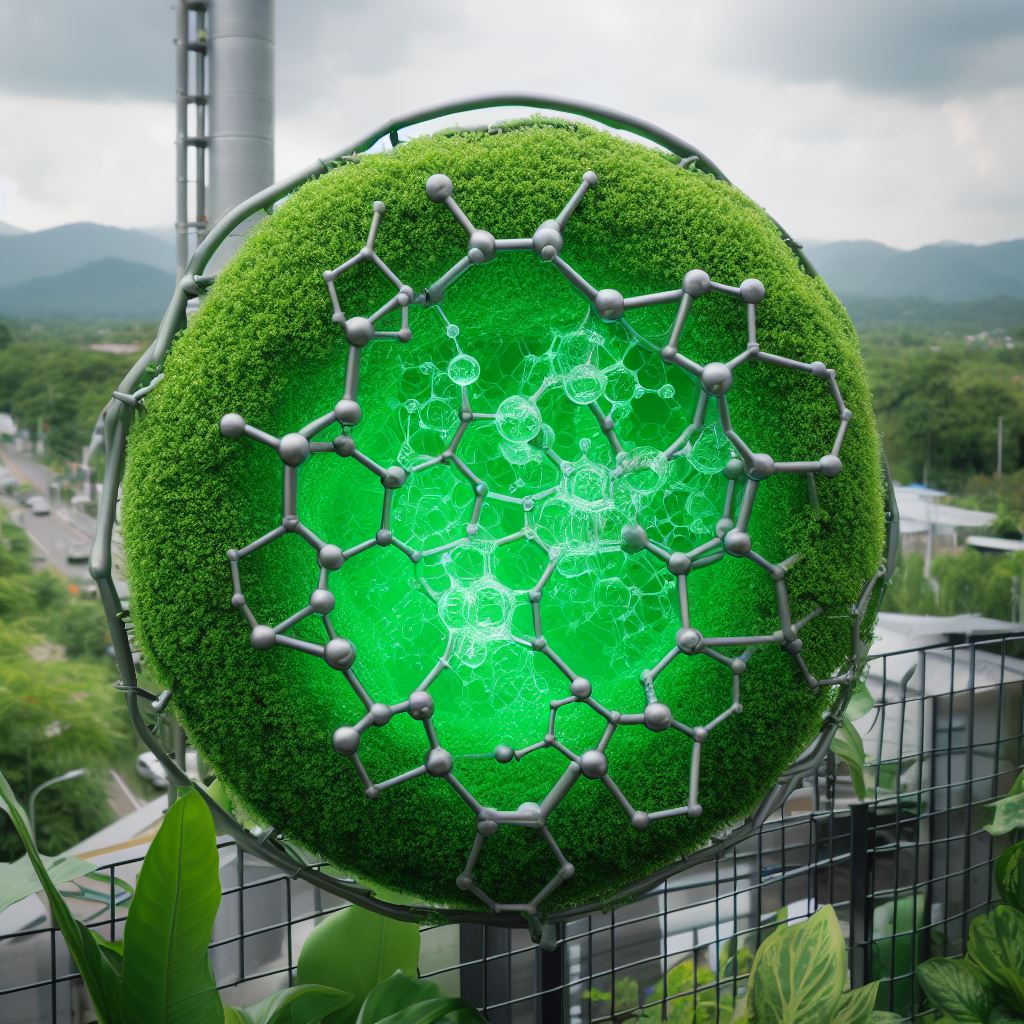
Stainless steel, a crucial material in various industries, faces limitations due to the conventional Cr-based single-passivation mechanism. This study unveils a sequential dual-passivation mechanism in Mn-contained stainless steel, enhancing anti-corrosion properties. The strategy extends the passive region of stainless steel to high potentials, making it a potential anodic material for green hydrogen production via water electrolysis.
Related Posts