Using Material Flow Cost Accounting (MFCA) to Cut Carbon Footprints

Table of Contents
Companies across industries are under pressure to reduce their environmental impact while staying profitable. One tool gaining momentum is Material Flow Cost Accounting (MFCA). Unlike traditional accounting systems that only track financial transactions, MFCA connects material and energy flows with their associated costs, making inefficiencies visible and measurable.
This approach not only helps reduce waste and improve resource efficiency but also directly contributes to lowering a company’s carbon footprint.
What is MFCA?
MFCA is a method within Environmental Management Accounting that tracks the physical flow of materials (in kilograms, liters, or other units) alongside the monetary costs attached to them. It distinguishes between:
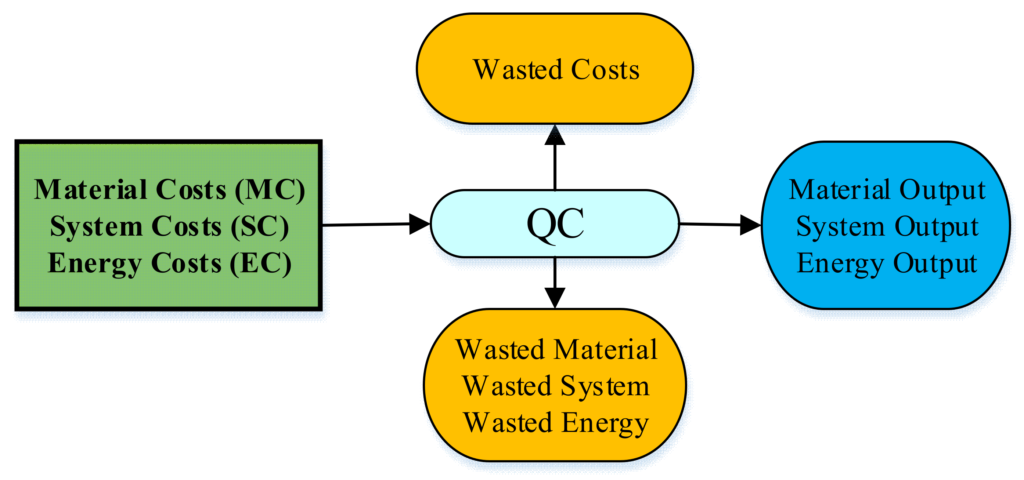
- Intended output – finished products
- Unintended output – waste, by-products, or inefficiencies
By assigning costs to both categories, MFCA reveals the hidden financial and environmental burden of waste. This transparency helps businesses make smarter operational and sustainability decisions.
Why MFCA Matters for Sustainability
Traditional accounting systems often overlook the real cost of material losses and excess energy use. MFCA closes this gap by showing companies how inefficiencies increase both expenses and emissions.
Key benefits include:
- Identifying hotspots of material and energy waste
- Improving communication across departments and suppliers
- Supporting low-carbon strategies with clear data
- Aligning financial performance with sustainability targets
Case Study: MFCA in the Wine Industry
A winery in Spain adopted MFCA to monitor its carbon footprint across the value chain. The project unfolded in six phases:
- Analyze energy use and emissions across the production and supply chain using Life Cycle Assessment (LCA).
- Link CO₂ emissions to products to calculate per-unit carbon intensity.
- Develop an online program for real-time emissions tracking.
- Engage stakeholders, including technical staff, cooperative farmers, and supply chain partners.
- Integrate the system with accounting and reporting tools.
- Report results through internal and external communication systems.
The outcomes were significant:
- Carbon reduction: Monitoring revealed high emissions from glass production, prompting targeted improvements.
- Operational efficiency: Inefficient machinery was repaired or replaced, reducing energy costs.
- Supply chain collaboration: Farmers gained insights into their energy use and became more engaged in sustainability.
- Market advantage: The winery could now label and report product-specific carbon footprints, strengthening its reputation in environmentally conscious markets.
This case shows how MFCA not only reduces emissions but also improves profitability and stakeholder relationships.
Looking Ahead: MFCA as a Business Standard
As sustainability reporting becomes stricter, tools like MFCA will play a crucial role in corporate strategy. Policymakers are already encouraging businesses to adopt material waste indicators, and companies that act early will gain a competitive edge.
Going forward, MFCA can help organizations:
- Track carbon emissions per product line
- Design near-zero emission offerings
- Compare sustainability performance across industries
- Meet ESG and net-zero commitments more effectively
MFCA is more than an accounting tool; it is a bridge between environmental responsibility and business performance. By making waste and inefficiency visible in both physical and financial terms, companies can cut costs, strengthen supply chains, and significantly reduce their carbon footprints.
What is Material Flow Cost Accounting (MFCA)?
MFCA is a sustainability-focused accounting method that tracks material and energy flows within a business. Instead of only calculating financial costs, it also identifies hidden environmental costs, waste, and inefficiencies in production.
How is MFCA different from traditional cost accounting?
Traditional accounting mainly focuses on direct financial transactions. MFCA, on the other hand, highlights the physical flow of materials and energy, showing how waste and inefficiencies translate into real financial losses.
Why should businesses adopt MFCA?
Reduce material waste
Improve energy efficiency
Lower production costs
Enhance sustainability performance
Meet ESG and reporting requirements
Is MFCA only useful for large corporations?
No. MFCA can benefit businesses of all sizes, from small manufacturers to large multinational corporations. Smaller businesses can especially gain by cutting hidden costs that often go unnoticed.
Can MFCA help in achieving sustainability goals?
Yes. By identifying inefficiencies and waste, MFCA enables businesses to make more resource-efficient choices, helping them align with sustainability targets, reduce their carbon footprint, and improve supply chain responsibility.
How does MFCA connect to profitability?
Every unit of wasted material or energy represents money lost. By reducing waste, businesses directly improve profit margins while also gaining a competitive edge in sustainability reporting.
What are the first steps to implement MFCA in a company?
Map material and energy flows across operations
Identify inputs, outputs, and waste streams
Assign financial values to material losses
Develop strategies to reduce inefficiencies
Monitor progress and refine processes continuously